- Consistent Air Quality
- Utilizes advanced filtration technology
- Enhanced Aseptic Zones
- Flexibility in various application
- Ergonomic design
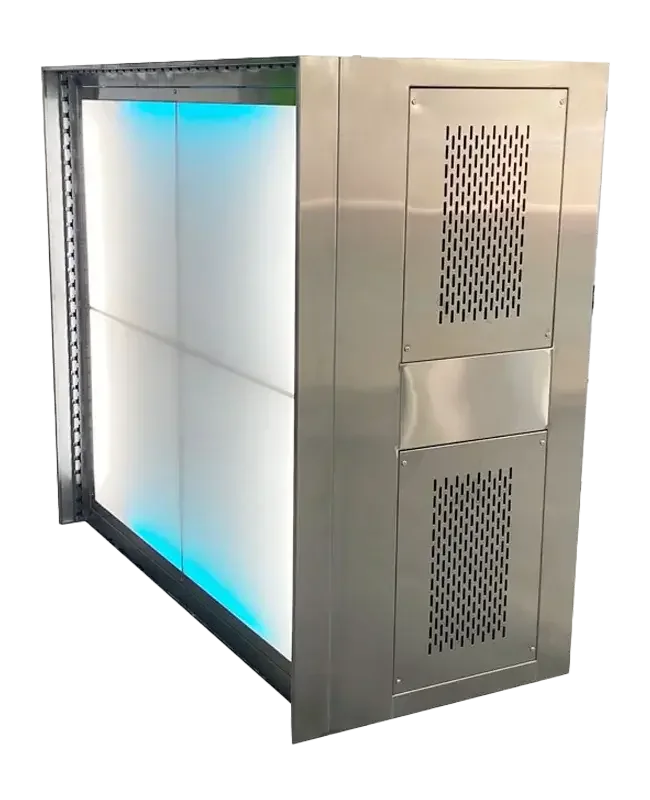
Design your custom Modular Cleanrooms with YNClean Manufacturer. Select your clean room's specifications to begin the design process and receive a tailored quote.
At YNClean, our Schematic Design for cleanrooms stands out due to our collaboration with top design schools, our team of experienced engineers, and our deep understanding of industrial processes, regulatory requirements, and technological advancements. Trust YNClean to deliver solutions that not only meet but exceed your expectations, leveraging the best in design and engineering.
Our in-house manufacturing capabilities empower us to maintain strict control over the quality of every component and leverage cutting-edge technologies that adapt to the evolving needs of your industry and benefit from the latest advancements in air purification, cleanroom design, and modular operating room technology.
Our ability to offer On-Site Installation stems from our skilled and experienced installation team, equipped with comprehensive knowledge of our products and systems. We ensure seamless integration into your existing infrastructure, adhering to all safety and regulatory standards. Our commitment to quality and precision guarantees that your installation is completed efficiently and to the highest standards, minimizing downtime and maximizing performance.
Between meeting ISO 8/Class100,000 to ISO 5/Class100 standards, maintaining building compliance, and supporting your operations over the long term, YNClean will be your premier supplier of the correct modular cleanroom.
Cleaning Constructure
We provide complete turnkey modular cleanroom solutions for your project through manufacturing, supplying, and installing
Solution One
Studies have consistently shown that directing clean air vertically downward creates a more effective cleanroom environment. High-efficiency fans regulate the speed and direction of filtered air, and through High-Efficiency Particulate Arrestor (HEPA) or Ultra Low Penetration Air (ULPA) filters capture almost all particulates, pushing contaminants toward plenums for either outside disposal or recirculation back through the filter.
At YNClean, our Schematic Design for cleanrooms stands out due to our collaboration with top design schools, our team of experienced engineers, and our deep understanding of industrial processes, regulatory requirements, and technological advancements. Trust YNClean to deliver solutions that not only meet but exceed your expectations, leveraging the best in design and engineering.
Our in-house manufacturing capabilities empower us to maintain strict control over the quality of every component and leverage cutting-edge technologies that adapt to the evolving needs of your industry and benefit from the latest advancements in air purification, cleanroom design, and modular operating room technology.
Cascading airflow is to utilize strategic air pressure differentials to prevent contamination, called Pressure Cascade Cleanroom Design. Cascading airflow consists of multiple interconnected rooms. Each room has a different Pressure that generates pressure Gradients: The cleanest areas boast the highest air pressure, while less critical zones have progressively lower pressure. This creates a directed flow, pushing contaminants from cleaner to less clean environments.
Industrial Clean Room Airflow Equipment
Solution Two
The working principle of Cleanroom Ceiling Panel is to close FFU module/ACU Ceiling Module slots to prevent air leakage and improve the cleanliness of the clean room. The air needs to be filtered and purified through the FFU/ACU Module to maintain cleanliness. Unused slots need to be installed with Ceiling Panel plates to prevent air leakage and effect the cleanliness of the clean room.
Self-supported ceiling grids are independent of the building's structural ceiling. They use their frame to support the ceiling panels and other components. The grid system stands on its framework and does not rely on the structural ceiling that doesn't require attachment to the building's ceiling or walls. Provides flexibility in load distribution and can be used in modular cleanroom setups.
A Hanging Ceiling Grid (also sometimes called a Suspended Ceiling Grid) is a traditional type of ceiling system used in cleanrooms. Unlike self-supported grids, hanging grids rely on the building's structural elements for support. Hanging grids utilize cables, rods, or other support elements attached to the building's structure above the cleanroom. This allows the ceiling panels to hang freely below.Typically constructed from cleanroom-grade materials like extruded aluminum. These materials offer durability, ease of cleaning, and minimal particle shedding. Similar to self-supported grids, hanging grids often come in pre-fabricated modules that can be assembled to create the desired ceiling size and layout.
The Walkable Grid Ceiling System in cleanrooms ensures safe, easy access to the plenum area for maintenance, inspections, and equipment installations like HVAC systems. Engineered to support personnel and tools, it maintains cleanliness by preventing contamination. Customizable for specific room dimensions and load needs, it features interchangeable panels for efficient installation and replacement.
The Light-Weight Ceiling System uses materials and methods to reduce the overall weight of the ceiling. It employs a framework of lightweight metals, typically aluminum, to support the ceiling tiles, which are made from materials like mineral fiber, fiberglass, or metal. Hangers and wires attach the grid system to the building structure.
Solution Three
Cleanroom ceiling lights are specialized fixtures designed to illuminate controlled environments without compromising cleanliness. Constructed with materials that minimize particle shedding and offer easy cleaning, these lights ensure optimal lighting conditions while maintaining the cleanroom's integrity. Key features include efficient LED technology, antimicrobial coatings, Low Particle Emission, Sealed and Flush-Mounted Designs, Uniform Illumination, airtight enclosures, easy Maintenance, and Compliance with Cleanroom Standards.
Solution Four
Cleanroom wall panels are specialized components designed for controlled environments. They are constructed to minimize particle release, resist chemicals, prevent static buildup, and be easily cleaned. Made from materials like stainless steel, aluminum, composite, vinyl, or PVC, these panels can be hardwall, softwall, or modular. Featured with Smooth and Non-Porous Surfaces, Durability and Strength, Seamless Integration Modular Design, Thermal and Acoustic Insulation, and Compliance with Cleanroom Standards.
Solution Five
Cleanroom doors are specialized entryways designed to maintain the controlled environment within a cleanroom. Their specialized features, such as airtight seals, smooth surfaces, and interlocking systems, are essential for preventing contamination and ensuring the smooth operation of cleanroom facilities. They are engineered to minimize particle and microbial contamination while ensuring smooth and efficient access.
Solution Six
The primary goal of cleanroom contamination control is to prevent and mitigate the introduction, generation, and retention of contaminants within the cleanroom. This involves a combination of engineering controls, administrative practices, and specialized equipment. Using specialized equipment like air showers and pass-through boxes, along with stringent administrative controls, it is possible to significantly reduce the risk of contamination significantly, ensuring the integrity and quality of products and research outcomes. These environments are essential in industries such as pharmaceuticals, biotechnology, semiconductor manufacturing, and aerospace, where even minute contaminants can significantly impact product quality and safety.
Cleanroom equipment includes air showers, Fan Filter Units (FFU), Pass-through boxes, laminar flow workstations, fume hoods, HEPA filters, replacement HEPA filters, Biosafety Cabinets, Hepa boxes, etc. When choosing cleanroom equipment, you should consider what applications you will be using the cleanroom for, what specifications the room will need to meet, what equipment you will need for your cleanroom experiments, and what size cleanroom will be required to accommodate that equipment.